With a strong desire to cultivate a career in a dynamic and forward-thinking environment, I aim to leverage my abilities to embrace challenges, foster innovation, and unlock my full potential. By seeking opportunities that offer continuous professional growth, I aspire to push boundaries and explore new horizons, contributing to the ever-evolving landscape of possibilities.
Research Area
Thermal and Fluid Engineering
Nanofluids
Heat Exchanger
Phase Change Materials
Heat Transfer
Polymers
Fire Simulation, CFAST, FDS
WORK EXPERIENCE
- POSTDOC: Chungnam National University, South Korea (Aug, 2022- Jan,2024)
- POSTDOC: Chosun University, South Korea (Aug,2021-July,2022)
- GUEST FACULTY: Mechanical Engineering Department, Tezpur University, India (Feb,2021- June,2021)
- ASSISTANT PROFESSOR: Mechanical Engineering Department, KSVCEM, Bijnor, India (Aug,2014- June,2015)
EDUCATION
Ph.D.: Indian Institute of Technology (Banaras Hindu University), Varanasi, India,(2015- 2020)
M. Tech: National Institute of Technology, Jamshedpur, Jharkhand, India, (2012-2014)
My Latest Work
1. Identification of primary input parameters affecting evacuation in ventilated main control room through CFAST simulations and application of a machine learning algorithm to replace CFAST model
Abstract
Accurately predicting evacuation time in a ventilated main control room (MCR) during fire emergencies is crucial for ensuring the safety of personnel at nuclear power plants. This study proposes to use neural networks alongside consolidated fire and smoke transport (CFAST) simulations to serve as a surrogate model for physics-based simulation tools. Our neural networks can promptly predict the evacuation time in MCRs, proving to be a valuable asset in fire emergencies and eliminating the need for time-consuming rollouts of the CFAST simulations. The CFAST model simulates fire and evacuation scenarios in a ventilated MCR with variations in input parameters such as door conditions, ventilation flow rate, leakage area, and fire propagation time. Target output parameters, such as hot gas layer temperature (HGLT), heat flux (HF), and optical density (OD), are used alongside standardized evacuation variables to train a machine learning model for predicting evacuation time. The findings suggest that high ventilation flow rates help to dilute smoke and discharge hot gas, leading to lower target output parameters and quicker evacuation. Standardized evacuation variables exceed the required abandonment criteria for all door conditions, indicating the importance of proper evacuation procedures. The results show that neural networks can generate evacuation times close to those obtained from CFAST simulations.
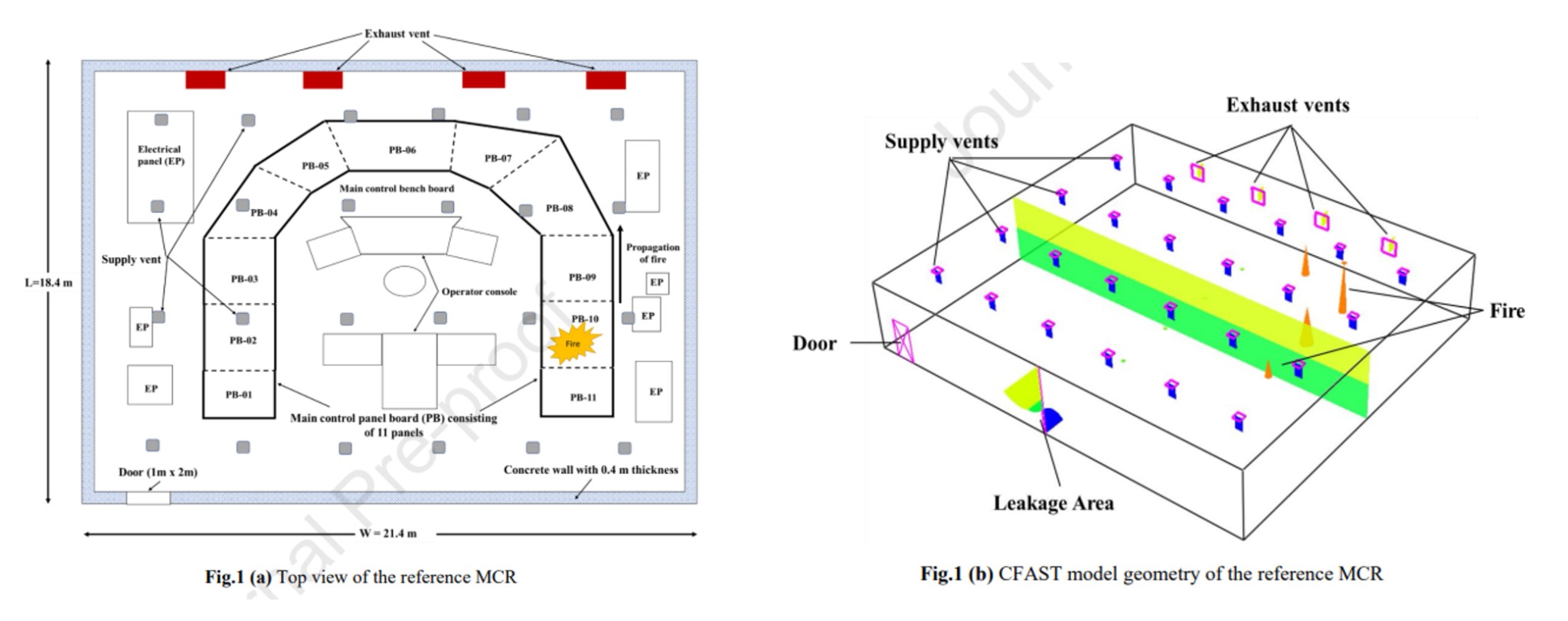
2. Enhanced ignition and combustion performance of boron-based energetic materials through surface modification and titanium dioxides coating
ABSTRACT
The present study focuses on the removal of ineffective hydroxyl surface (B–OH) of the shell of pristine boron (B) particles, followed by its modification using a low-cost, eco-friendly, and non-hazardous ethylene glycol (EG). Subsequently, very small-sized titanium dioxide (TiO2) particles are coated onto the boron surface by adding titanium tetraisopropoxide (TTIP) precursors at room temperature. Characterization techniques were employed to investigate the structure and morphology of these materials. FTIR, XPS, and TEM analysis reveal that EG effectively removes ineffective boron hydroxyl surfaces and modifies the surface through passivation by its surface functionalities. Furthermore, EG assists in the coating very small-sized TiO2 particles on the boron surface. Thermal stability tests show that the modified boron surface and TiO2-coated boron surface exhibit earlier oxidation of the core boron compared to pristine boron. This enhanced capability for earlier oxidation of core boron was further investigated in the shock tube and bomb calorimeter for measurement of ignition delay time and heat of combustion. The findings demonstrate that room temperature synthesized TiO2-coated B particles (ignition delay time of ~181 μs and heat of combustion of ~17.3 kJ/g) outperform pristine B particles (ignition delay time of ~284 μs and heat of combustion of ~13.2 kJ/g). This improvement is attributed to the removal of ineffective boron hydroxyl surfaces, surface modification, uniform coating with very small TiO2 particles, the catalytic effect of TiO2 on oxygen diffusion, and effective oxidation of core boron. This study suggests that efficient energetic material can be achieved at room temperature with no potential harm to the environment.
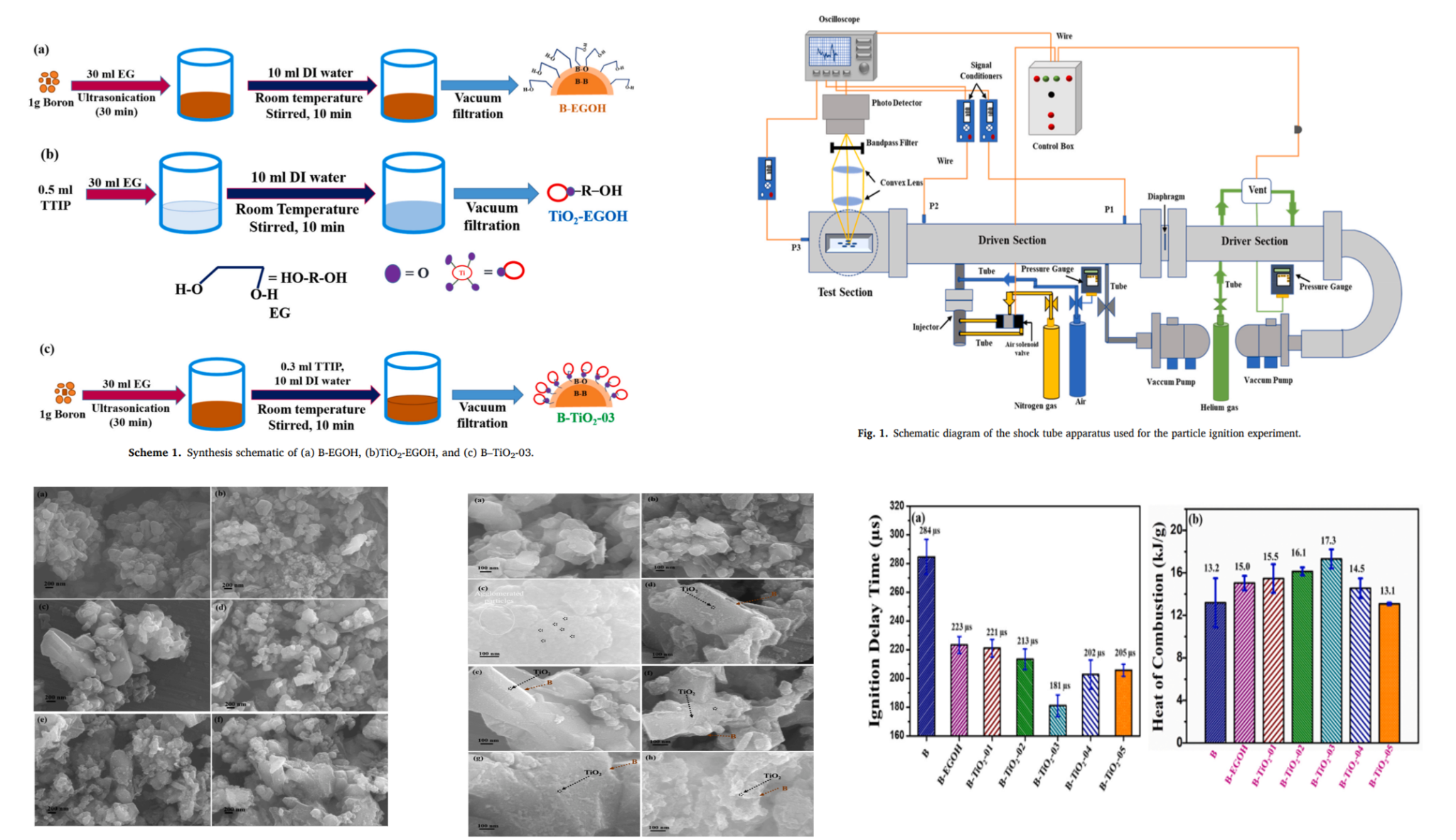
3. Hydrothermal performance comparison of modified twisted tapes and wire coils in tubular heat exchanger using hybrid nanofluid
ABSTRACT:
A comparative experimental study to examine the hydrothermal behaviors of the double tube heat exchanger with various modified twisted tape and wire coil inserts is performed using Al2O3+MWCNT hybrid nanofluid. The investigation is performed for Reynolds number of 8000–40000, nanofluid flow rate of 5–25 lpm and volume concentration of 0.01%. The effects of using various enhancers (V-cut twisted tapes and tapered wire coils) and hybrid nanofluid on the hydrothermal characteristics are assessed for different enhancer arrangements such as different twist ratios, V-cut depth ratios, V-cut width ratios, converging type (C-type) wire coil, diverging (Dtype) wire coil and converging-diverging type (C-D type) wire coil. The test reveals that the pressure drop and heat transfer coefficient increase with reducing twist ratio, increasing depth ratio and reducing width ratio. Dtype wire coil exhibits higher heat transfer performance with the penalty of pressure drop than that of other arrangements. V-cuts twisted tape of minimum twist ratio, maximum depth and width ratios yields maximum PEC and FOM. V-cut twisted tapes show a higher performance index than the tapered wire coil as the augmentation in pressure drop is slightly significant. D-type wire coil shows the minimum value of entropy generation among all other arrangements.
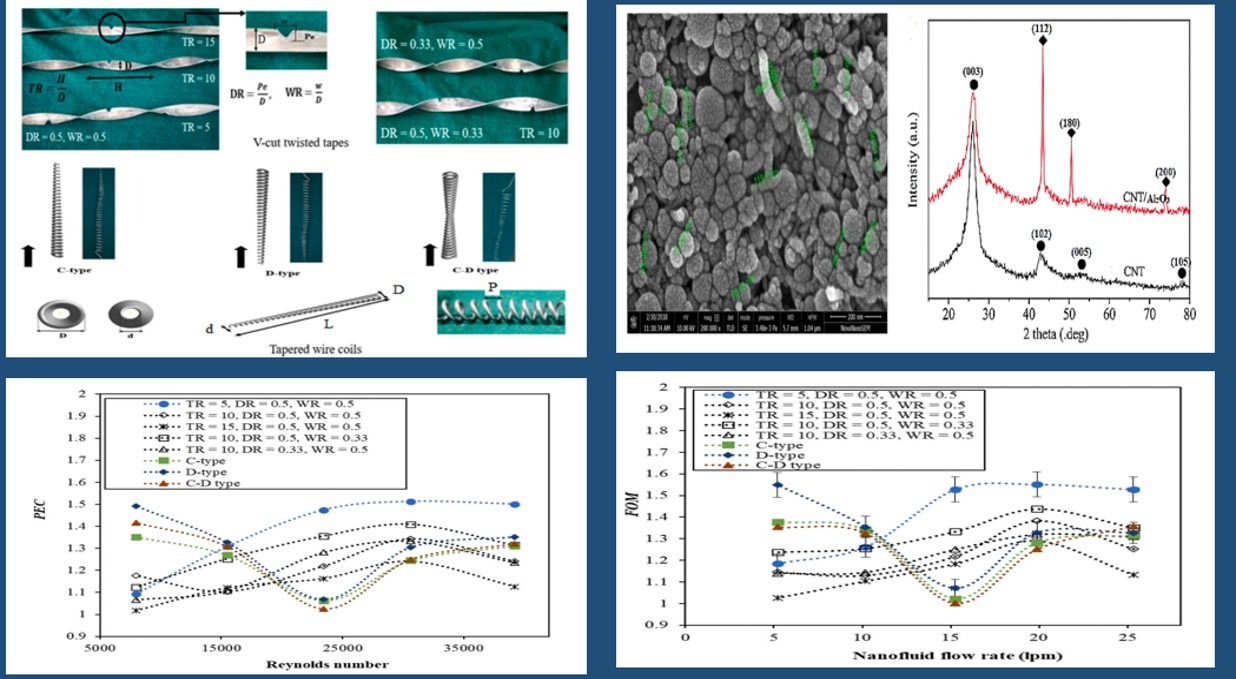
4. Thermal and thermo-hydraulic behaviour of aluminagraphene hybrid nanofluid in minichannel heat sink: An experimental study
ABSTRACT:
Thermal and pressure drop aspects of a minichannel heat sink have been investigated experimentally using distilled water as base fluid with alumina, graphene and alumina-graphene hybrid composition at 0.01% volume concentration. The reasons to select alumina-graphene as a potential nanomaterials combination for hybrid nanofluids are as: (i) thermal conductivity enhancement and (ii) to investigate the effect of morphology (shape and size of nanoparticles). Alumina (Al2O3) is oxide and has spherical shape whereas graphene is allotrope of carbon and has platelet shape. To examine the effect of different nanoparticles (in terms of shape, size and properties) dispersed hybrid nanofluid on hydrothermal bahaviour is an interesting study. Effects of Reynolds number (80-450), flow rate (0.1-0.5 L/min) and fluid inlet temperature (20-40?C) are studied. The effects of uniform heat flux of 50 and 66.7 W/cm2 on hydrothermal behaviour of a minichannel are also examined. The increment in convective heat transfer coefficient (HTC) is 30.93% at 30oC with graphene/water composition nanofluid than water base fluid. A penalty of 23.82% has been observed in pressure drop with graphene/water nanofluid over base fluid. As inlet temperature increases, Nusselt number (Nu) increases while adverse effect is found in case of friction factor. Performance evaluation criteria (PEC) has been observed more than 1 for all nanofluids and hybrid nanofluids, which ensured that nanofluids act as a better electronic cooling agent than water. Al2O3 + graphene hybrid nanofluid delivers optimum comparison factor (HTC to pressure drop ratio) and lower entropy generation rate among used working fluids. Graphene/water nanofluid yields less comparison factor compared to other working fluids irrespective of high HTC. h/Δp is favourable for nanofluid of unlike particles of hybrid composition (in terms of particle size, properties and shape) as compared to mono nanofluid and hybrid nanofluid having similar particles.
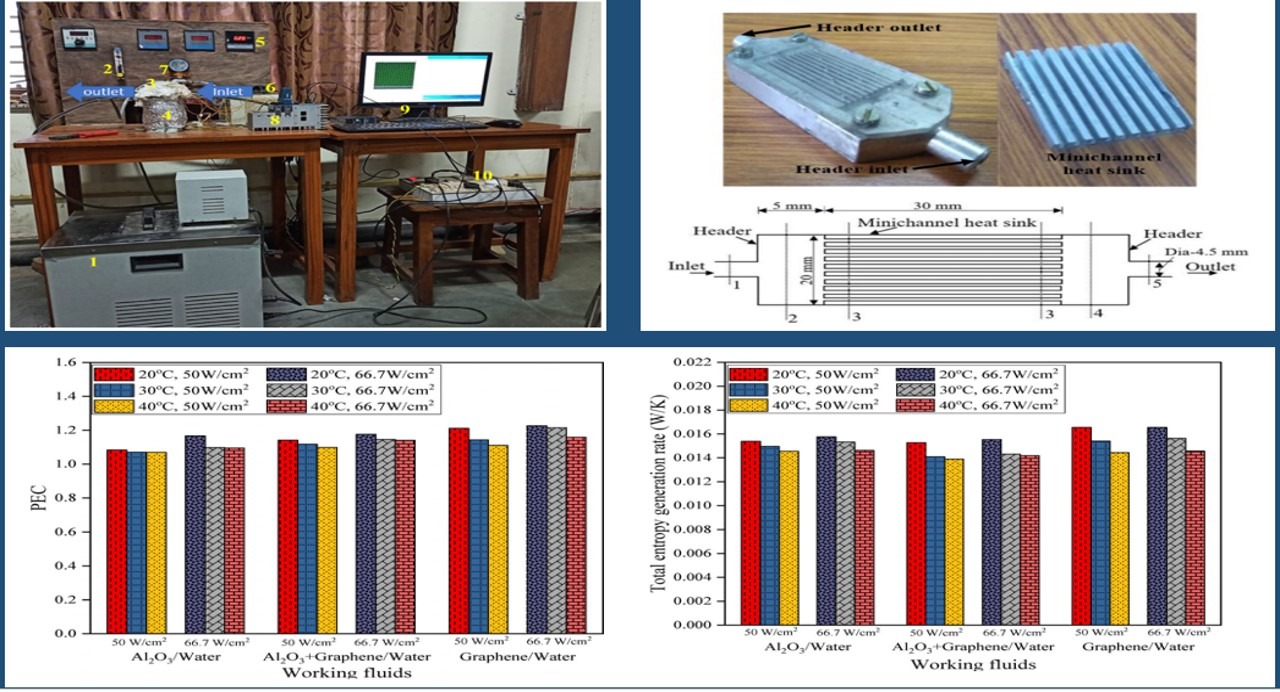
5. Thermohydraulic behavior of concentric tube heat exchanger inserted with conical wire coil using mono/hybrid nanofluids
ABSTRACT:
The experimental studies with a new type of enhancer, conical wire coil insertion in the concentric tube heat exchanger using water-based mono (Al2O3 and CNT) and hybrid (Al2O3 + CNT) nanofluids, flowing in the inner tube, are conducted to examine the effect on thermohydraulic performance. The thermohydraulic performances are studied with various conical wire coil configurations (converging, diverging and converging-diverging coils). The outcomes indicate that the diverging wire coil insert exhibits better thermohydraulic performance as compared to other wire coil arrangements. In comparison to DI water in the plain tube (without insert), the maximum Nusselt number enhancements for diverging, converging-diverging and converging wire coil inserts are 171%, 152% and 139%, respectively. Similarly, the friction factor is increased up to 106%, 92% and 72%, respectively, for diverging, converging-diverging and converging wire coil inserts. In all conditions, it is found that the entropy generation of DI water is higher than that of mono/hybrid nanofluids. The thermal performance factor is observed more than one with all mono/hybrid nanofluids and wire coil inserts, indicating a promising combination.
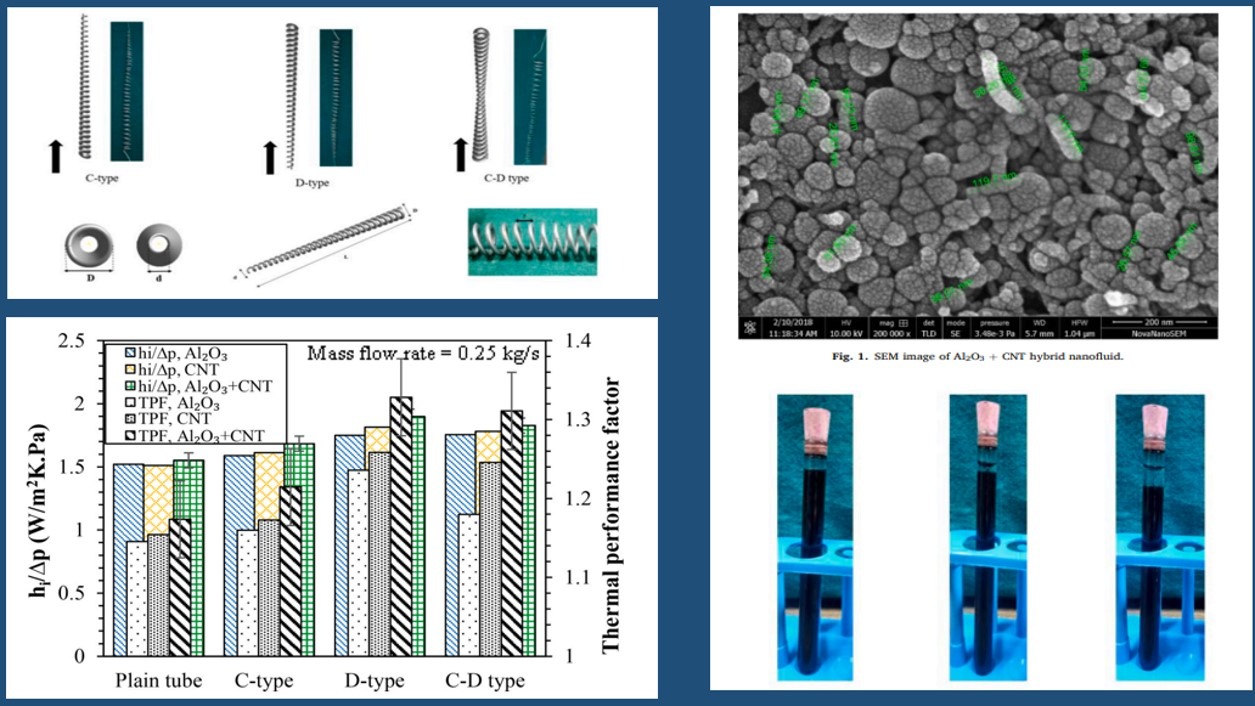
6. Improving hydrothermal performance of double‑tube heat exchanger with modifed twisted tape inserts using hybrid nanofuid
ABSTRACT:
The experimental studies on Al2O3+TiO2 hybrid nanofluid flowing under the turbulent condition in a double-tube heat exchanger with various modified V-cuts twisted tape inserts are performed to study the hydrothermal characteristics. The hybrid nanofluid is prepared with a volume concentration of 0.1% by dispersing Al2O3 and TiO2 nanoparticles by equal volume ratio in distilled water. The effect of using twisted tape turbulator (with and without V-cuts) and hybrid nanofluid on the heat transfer and pressure drop characteristics are evaluated for different twist ratios, V-cut depth ratios, V-cut width ratios and hybrid nanofluid inlet temperatures. Results show that Nusselt number as well as friction factor increases with the decrease in twisting ratio, increase in depth ratio, decrease in width ratio and decrease in nanofluid inlet temperature. Maximum improvements in 132% for Nusselt number and 55% for friction factor are obtained as compared to that for the water in the tube without twisted tape. The values of thermal performance factor and entropy generation ratio are greater than unity for hybrid nanofluid for all modified twisted tape inserts.
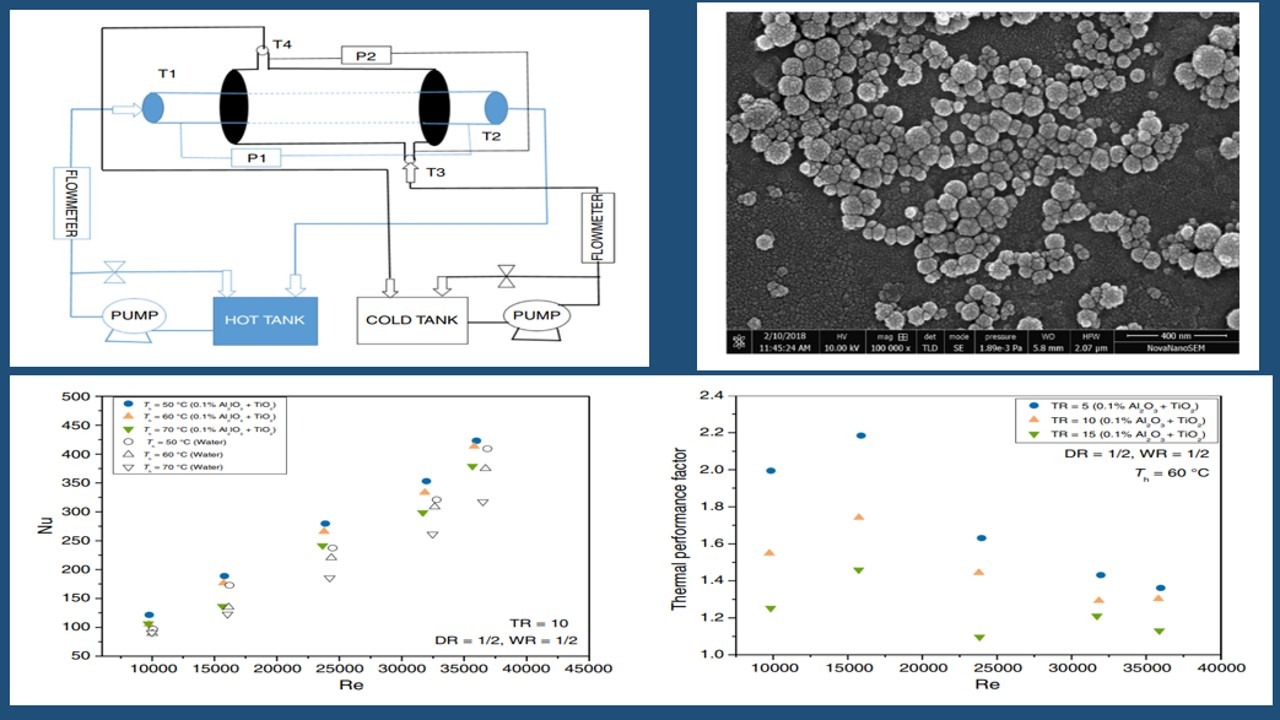
7. Experimental hydrothermal characteristics of concentric tube heat exchanger with V-cut twisted tape turbulator using PCM dispersed mono/hybrid nanofluids
ABSTRACT:
Impact of using V-cuts twisted tape insert and phase change material (PCM) dispersed mono or hybrid nanofluid on the hydrothermal characteristics of the double tube heat exchanger is experimentally investigated. Water-based Al2O3 and PCM nanofluids and Al2O3+ PCM hybrid nanofluid with different concentrations are used in inner tube. Influences of various geometric parameters of V-cuts twisted tape insert on heat transfer, pressure drop and entropy generation are investigated. Results reveal that heat transfer and pressure drop increase with the increase in particle concentration and decrease in twisting ratio. A higher V-cut depth ratio or lower width ratio yields more heat transfer and pressure drop
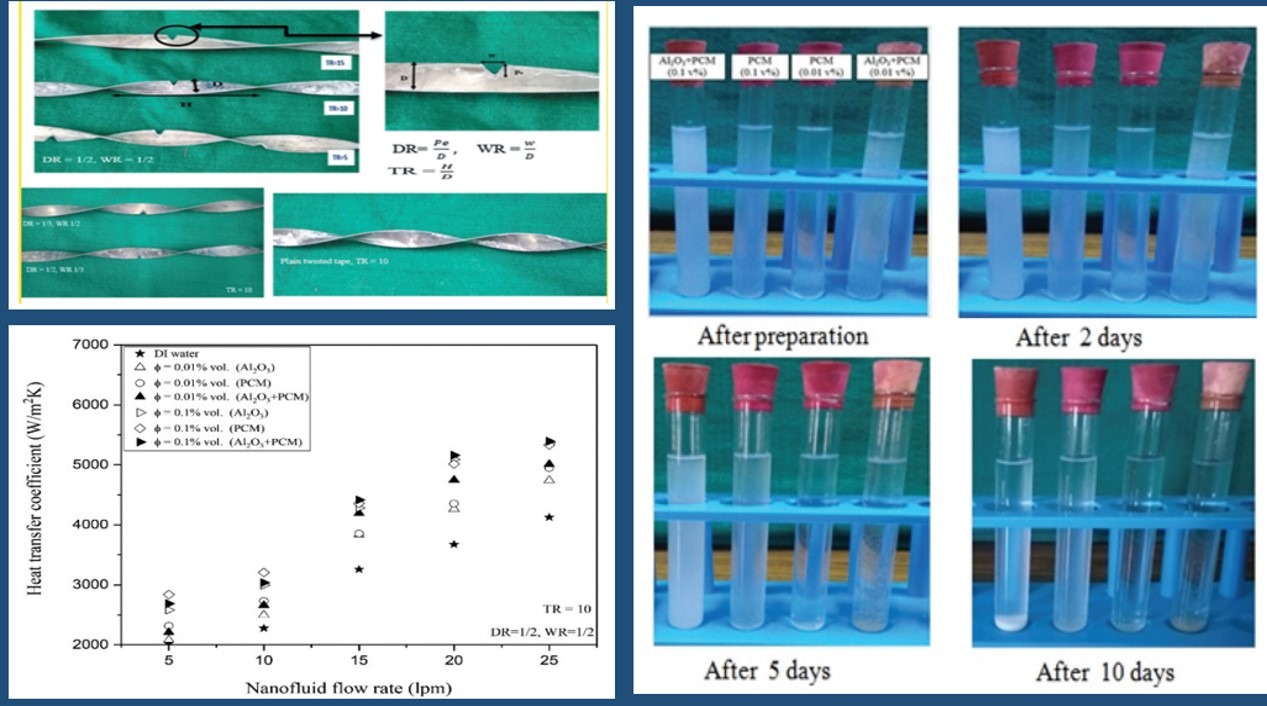
8. Improving hydrothermal performance of hybrid nanofluid in double tube heat exchanger using tapered wire coil turbulator
ABSTRACT:
Tapered wire coil insert is proposed as a novel enhancer in the double tube heat exchanger and experimental studies on Al2O3 + MgO hybrid nanofluid flowing under the turbulent condition are performed to investigate the hydrothermal characteristics. Effects of using tapered wire coil turbulator and hybrid nanofluid on the hydrothermal behaviors are examined for different coil configurations (Converging (C) type, Diverging (D) type and Conversing-Diverging (C-D) type) and hybrid nanofluid inlet temperatures and volume flow rates. Results show that D-type wire coil insert promotes better hydrothermal performance as compared to C-type and C-D type. Nusselt number and friction factor of hybrid nanofluid using D-type, C-D type and C-type wire coil inserts enhance up to 84%, 71% and 47%, and 68%, 57% and 46%, respectively than that of water in tube without insert. The entropy generation of hybrid nanofluid is lower than that of base fluid in all cases. The thermal performance factor for hybrid nanofluid is found more than one with all inserts. The thermal performance factor is observed a maximum of 1.69 for D-type coil. The study reveals that the hybrid nanofluid and tapered wire coil combination is promising option for improving the hydrothermal characteristics of double pipe heat exchanger.
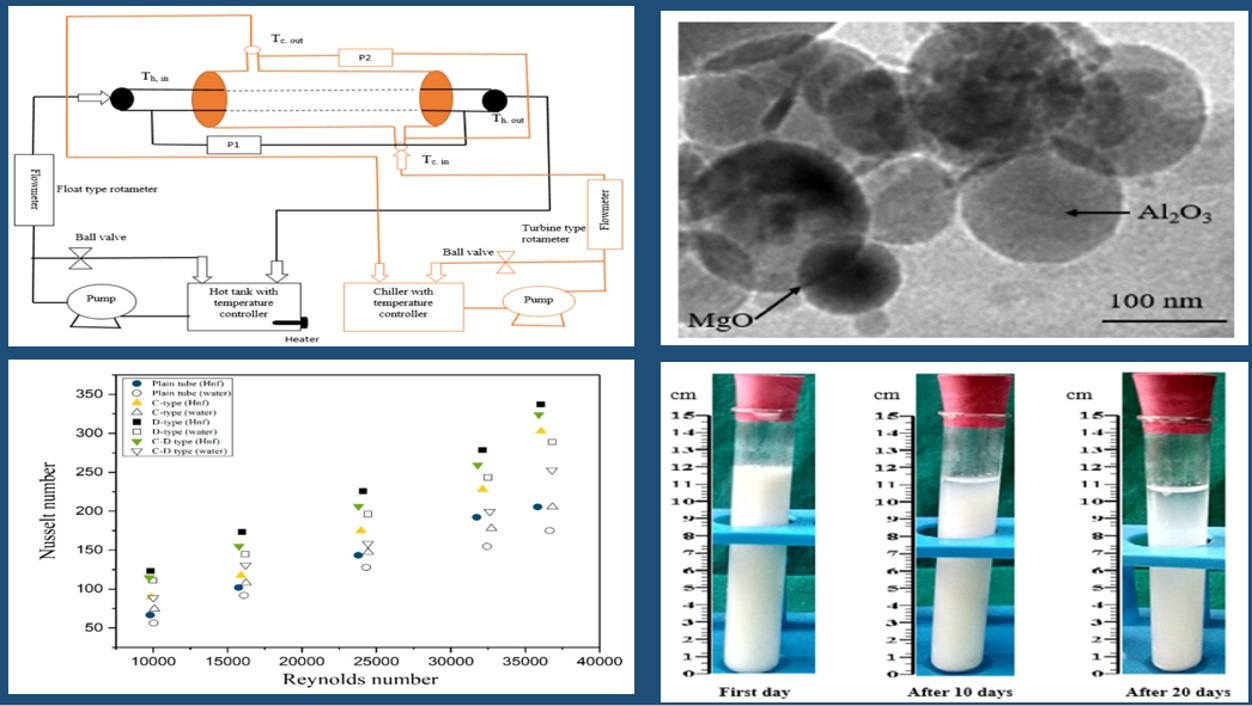
9. Energy, exergy and economic assessments of shell and tube condenser using hybrid nanofluid as coolant
ABSTRACT:
The energy, exergy and economic assessments of a shell and tube condenser of 580 MW nuclear power plant have been carried out using different water-based hybrid nanofluids such as Al2O3 + MWCNT, Al2O3 + Ag, Al2O3 + Cu and Al2O3 + TiO2 as coolant. The effect of nanoparticle concentration on reductions of coolant requirement, pumping power and operating cost has been investigated. The results reveal that Al2O3+MWCNT shows the highest reduction of coolant mass flow rate of 3.6%. The effectiveness of shell and tube condenser enhances with the addition of nanoparticles. The reduction of the pressure drop is maximum for Al2O3 + MWCNT hybrid nanofluid (5.8%) and minimum for Al2O3 + Ag (3.7%) at 1% volume concentration. Therefore, Al2O3 + MWCNT requires 11.2% less pumping power followed by Al2O3 + TiO2 (10.9%), Al2O3 + Cu (10.2%) and Al2O3 + Ag (9.6%) as compared to the base fluid. Al2O3 + Ag shows maximum (29.97%) and Al2O3 + MWCNT shows minimum (29.81%) second law efficiency at 1% volume concentration. Al2O3 + MWCNT hybrid nanofluid yields maximum saving of operating cost (11.1%) and Al2O3 + Ag shows minimum (9.62%) at 1% volume concentration. However, Al2O3 + Ag shows payback period about 247 years and Al2O3 + TiO2 about 9.8 years. Hence, the payback period needs to be reduced before practical implementation, which may be possible by reducing the nanoparticle cost and increasing nanofluid stability
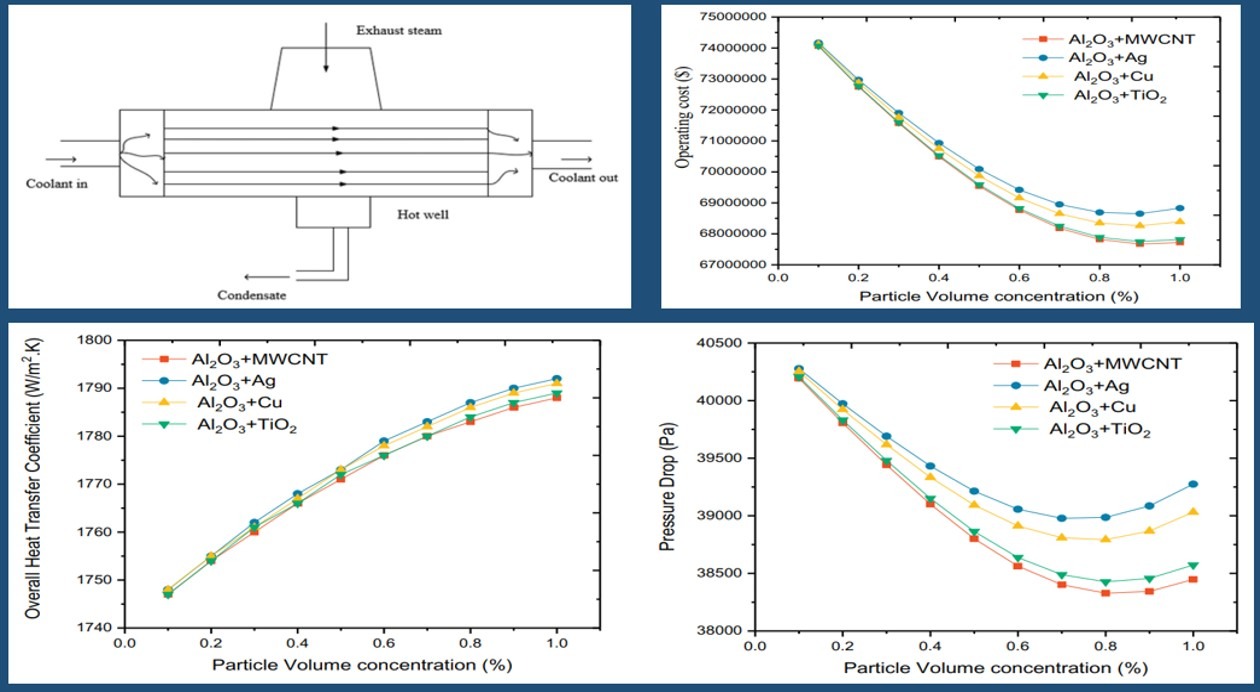
10. Improvement in Energy Performance of Tubular Heat Exchangers Using Nanofluids: A Review
ABSTRACT:
Both mono and hybrid nanofluids, the engineered colloidal mixture made of the base fluid and nanoparticles, have shown many interesting properties and become a high potential next generation heat transfer fluids in various heat exchangers for engineering applications. The present review focuses on improving the performance of tubular heat exchangers by using nanofluids. For this, the present review briefly summarizes the preparation, characterization and thermophysical properties (thermal conductivity, viscosity, specific heat capacity and density) of mono and hybrid nanofluids. Research works on heat transfer and pressure drop characteristics of nanofluids in the double tube and shell-tube heat exchangers with both straight and coiled tubes, and various engineering applications (power generation, refrigeration and air-conditioning, renewable energy, domestic cooling or heating, etc.) are well-grouped and thoroughly discussed. Physical mechanisms for the heat transfer enhancement using nanofluids are explored as well. Most of the studies reveal that there are significant enhancements in the heat transfer process and in the effectiveness of both straight and coiled tube heat exchangers with a slight increase in pressure drop using nanofluids. Hence, there is
an excellent opportunity to use nanofluids in tubular heat exchangers; however, high cost (high payback period) and stability are the main challenges for practical implementation. Finally, some useful recommendations are also provided.
